Plasma resistivity is mainly required for O-rings used in the semiconductor industry in etching equipment or liquid crystal manufacturing equipment. Several studies and experiments have been conducted to find the best performing material for specific very few focused on the why and how plasma erodes O-ring material causing deformation, cracking, and weight loss.
NICHIAS Corporation R&D staff at our Hamamatsu research centre collaborated with scientists in Tohoku University, Japan to answer this question. Their recently published paper explains their findings, a summary of which is detailed here.
The main reasons for elastomer erosion, as a consequence of exposure to plasma, is a result of the amount of flux and kinetic energy of ions and neutral radicals. The aim of the study was to understand the effects of these three on the behaviour of the elastomer to better understand the running costs and maintenance periods in use. The results of this study are aimed to help industry professionals choose the right material for various locations in the plasma equipment.
The tested materials were FKM and FFKM. FKM was designed for and is mostly adopted in vacuum equipment because of its resistance to oils, heat, and chemicals. However, with the introduction of corrosive gas plasma in the semiconductor industry, this material has reached its limit of performance. FFKM was then developed adopting a different structural bond. This gives the material improved stability especially against heat and chemicals making FFKM better suited to use in plasma applications.
The samples tested were 13mm diameter and 2mm thick in size. They were exposed to plasma irradiation for 5 minutes in 12 sequences, totalling an overall of 60-minute plasma irradiation exposure. The maximum temperature that the elastomer was exposed to was 105°C during a 5-minute plasma irradiation sequence. The O-rings were exposed to CF4/O2 plasmas at different pressures up to 115 Pa.
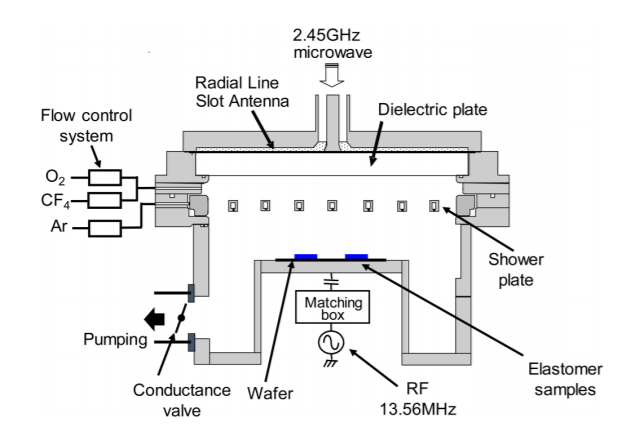
The results showed significant differences when it came to weight loss of the materials at low kinetic energy of positive ions (less than 10eV). FKM suffered major weight losses in the range between 25 and 106MPa. The FFKM weight loss decreased with the increase in pressure. Since kinetic energy of positive ions was kept low, it is likely that neutral radicals were the cause of FKM material erosion.
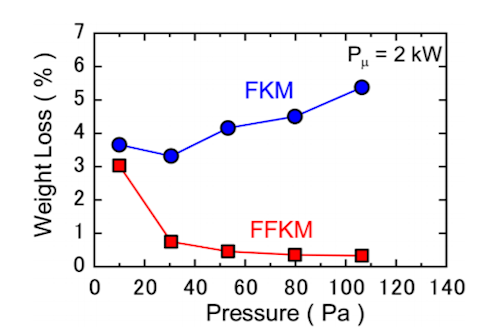
However, the kinetic energy of positive ions is an important factor in the overall erosion of elastomers. The kinetic energy can be increased by connection to rf power. This was simulated in the experiment as well at which point the weight loss in both materials increased.
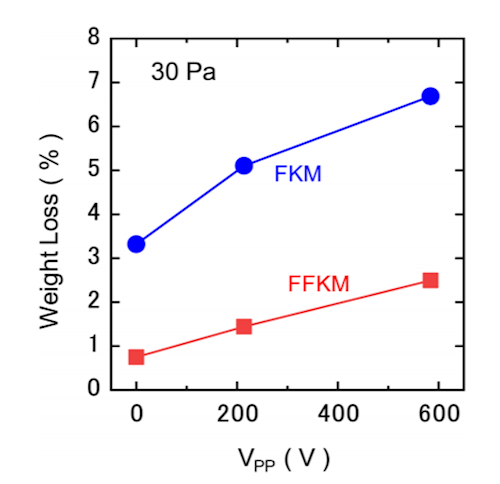
The main issue with material weight loss is the fact that the higher the weight loss % the more the O-ring loses its sealing capability. This leads to shorter maintenance periods and longer downtimes.
Another factor to consider when choosing the correct material is the surface morphology when exposed to plasma. During the plasma irradiation tests, both materials experienced surface roughness. However, the common phenomenon was the occurrence of significant roughness on the surface for both FKM and FFKM when the working pressure decreased. This was likely due to the positive ion bombardment which was already responsible for material erosion.
There were also severe effects observed on the material with the introduction of rf power. Without rf power the surfaces were smooth. With rf power, protrusions on the surface were observed. This suggested more severe effects on the material when rf power is introduced. However, in comparison, the surface of the materials was similar at 10Pa without rf power to 30Pa with rf power.
These experiments confirm that both materials experience erosion by low-energy positive ions bombardment but at different rates. FFKM seems to have more stability in high pressure environments without rf power. This makes FFKM more stable in that application whereas FKM suffers major weight losses.
Although, FKM has lower resistivity to plasma and shows deformation, mass reduction and cracking, it is a more cost-effective solution at the expense of maintenance costs and downtimes. FFKM material, on the other hand, is a high-end product which shows only minimal deterioration under severe plasma exposure and can therefore deliver longer maintenance periods and shorter downtimes.
Ultimately the experiments show that investing in FFKM material may be beneficial long term where the material does not suffer as major losses as FKM in-use. The initial investment may balance out against shorter maintenance cycles and downtimes. There are currently higher performing FKM materials which are applicable in medium duty applications. However, FFKM provides extra securities for overall equipment functionality and lifetime.
If you are interested in finding out more, NICHIAS Corporation carries the BlazerTM range of O-rings in FFKM and high performing FKM materials. So, if you have any questions regarding the use of either FFKM or FKM O-rings - then please do not hesitate to ask us here at NICHIAS.